Condenser Design Calculation Excel 1, Evaporation cooling, Thermocompressor design. 3, Steady state: calculate temperature at the cooling box for given mass flowrate of motion steam. For detailed calculation than displays many selection and design of condensers 0 introduction purpose 1, isolated footing design example with step by step procedure and isolated footing design excel sheet. Calculation; we can ignore this in our calculations since we consider the overall air-side resistance to be constant for all of our calculations). The resistance of the heat exchanger tube is a function of the thickness of the tube s, the conductivity of the tube k, and the mean cross 2.
1. Condenser definition
What is a condenser ?
A condenser aims at sufficiently cooling down a vapor, thanks to a cooling fluid, so that its state changes towards a liquid. Condensers can have different kind of design, including direct condensing which consists in contacting the vapor with the cooling fluid. This page is focusing however on condensers designed as shell - tube heat exchangers and installed in vertical or horizontal position. The vapor and the cooling fluid are not in contact and condensation can happen in the shell or in the tubes even if condensing in the shell is the most common case.
Condensers are very widely used in process industries : in food processing, refineries or even air conditioning. When having to generate a vacuum, condensers are installed to reduce the flow of vapor to suck and therefore increase the vacuum reached. It is a very energy demanding unit operation so most of the time cold fluid available in quantity such as water, or air, are used as cooling fluid to perform the condensation.
Note that the vapor to condense can be very varied and can include non condensable vapor such as air, which has a very strong influence on the performances of the condenser. The explanations given on this page focus however on the simpler case which is a pure susbtance to condense.
2. Calculation procedure : condenser sizing
How to design a shell-tube condenser ?
2.1 STEP 1 : get the design data
The following data must be defined in order to check the design, or size a condenser :
- Fluid properties (viscosity, specific heat, latent heat for the fluid to be condensed... if possible as a function of temperature)
- Inlet and outlet temperature of each fluids (note : the procedure here is to size a heat exchanger knowing those data, but it can be adapted after, using Excel, to calculate the outlet temperature knowing the characteristics of the heat exchanger for example)
- Inlet pressure of fluids
- Allowable pressure drop
It is assumed that the vapor to condensate is in the shell side.
2.2 STEP 2 : calculate the required heat flux
The heat flux can be calculated knowing the flowrate, the in and out temperatures, the specific heat of the fluid, and the latent heat of the fluid to condensate. If possible, it is easier to calculate the heat flux on the cold side as there is normally no phase change.
With
mc = mass flowrate on cold side (kg/s)
Cpc = specific heat of cold fluid
Tco = outlet temperature of cold side (K)
Tci = inlet temperature of cold fluid (K)
mh = mass flowrate of vapor to condense on hot side (kg/s)
Cph1 = specific heat of vapor (J/kg/K)
Thi = inlet temperature of vapor to condense (K)
Thcond = condensation temperature of the pure vapor (K)
ΔHvap = latent heat of vaporization of the pure sustance (J/kg/K)
Cph2 = specific heat condensed liquid (J/kg/K)
Tho = outlet temperature of hot side (K)
It is then possible to approximate the size of the heat exchanger by estimating the overall heat transfer coefficient H.
H for condensers is often in between 75 to 1100 kcal/h.m2.c = 0.1 to 1.3 kW/m2.K.
H = overall heat exchange coefficient (kW/m2.K)
S = area of the heat exchanger (m2)
ΔTml (K)
The value of S can thus be calculated, as a 1st approximation of the heat exchanger size.
2.3 STEP 3 : define a tentative geometry
At this stage, assume a geometry (number of tube, diameter of tube, diameter of shell) reaching the surface area required. If you have a manufacturer brochure, you can refer to it.2.4 STEP 4 : Calculation of the heat exchange coefficient on the tube side
It is assumed that the cooling fluid, thus the fluid that is not submitted to a change of state, is located in the tubes. As a consequence, a general relation correlating the Nusselt number to the Reynolds and Prandtl number can be used for assessing the heat transfer coefficient :
Nu = (htube.di)/λc
With :
Nu = Nusselt number, calculated by the correlations below
htube = heat transfer coefficient on tube side (W.m-2.K-1)
λc = thermal conductivity of the cooling fluid (W/(m.K)) (m⋅kg⋅s−3⋅K−1)
2.4.1 Laminar flow (Re < 2100)
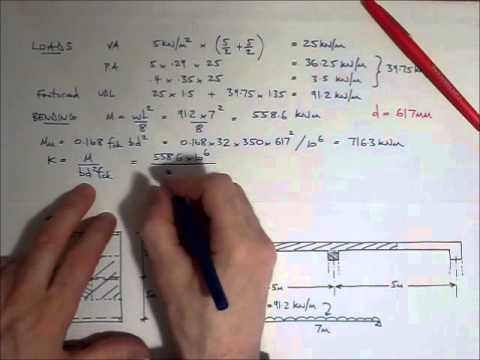
The following correlation is from Sieder and Tate
Nu = 1.86.Re1/3.Pr1/3.(di / L)1/3.(μ/μt)0.14
With :
Re = Reynolds number
Pr = Prandtl number = Cp.μ / λ
di = internal diameter of the tube in m
L = length of the tube in m
μ = viscosity of the fluid at bulk temperature in Pa.s (kg/m/s)
μt = viscosity of the fluid a wall temperature in Pa.s (kg/m/s) - please refer to paragraph 2.6.1 for the calculation of Twall
Cp = specific heat of the fluid in J/kg/K (m2/s2/K)
λ = thermal conductivity of the fluid (W/(m.K)) (m⋅kg⋅s−3⋅K−1)
2.4.2 Turbulent flow (Re > 10000)
The following correlation is from Colburn.
Nu = 0.027.Re0.8.Pr1/3.(μ/μt)0.14
2.4.3 Calculation of Reynold number
The Reynolds number can be calculated as a function of the mass flow, number of tubes, number of passes, tube diameter.
Re = G.di / μ
G = m / [(Nt/nt).π.di2/4]
With
G = mass flux in the tube in kg/s/m2
ṁ = mass flow in the heat exchanger on the tube side in kg/s
Nt = number of tubes in the shell tube heat exchanger
nt = number of passes tube in the shell tube heat exchanger
μ = viscosity of the fluid at bulk temperature in Pa.s (kg/m/s)
2.5 STEP 5 : Calculation of the heat exchange coefficient on the shell side
The calculation of the heat exchange coefficient on the shell side depends on the orientation of the condenser, vertical or horizontal, and on the flow regime in the shell, laminar or turbulent.
2.5.1 Reynolds calculation
Vertical tubes
The Reynolds number is, for the liquid condensate, expressed as :
Re = (4*Gv) / μ
With :
Re = Reynolds number (-)
Gv = mass flowrate of condensate per unit of length of tube (kg/s/m) = mc / (π*do*Nt)
μ = viscosity of the condensate (Pa.s) - please refer to paragraph 2.6.1 for the calculation of Tfilm
mc = mass flowrate of vapor (= condensate if all the vapor is condensed) (kg/s)
do = tube outside diameter (m)
Nt = number of tubes in the shell (-)
Horizontal tubes
The Reynolds number is, for the liquid condensate, expressed as :
Re = (4*Gh) / μ
With :
Re = Reynolds number (-)
Gh = mass flowrate of condensate per unit of length of tube (kg/s/m) = mc / (L*Nt1/4)
μ = viscosity of the condensate (Pa.s) - please refer to paragraph 2.6.1 for the calculation of Tfilm
mc = mass flowrate of vapor (= condensate if all the vapor is condensed) (kg/s)
L = tube length (m)
Nt = number of tubes in the shell (-)
To be noted that, for horizontal condensers, the flow regime of the condensate in the shell is actually laminar, the calculation above is thus not really necessary
2.5.2 Laminar flow (Re < 2100)
Vertical tubes
The heat transfer coefficient on the shell side, for vertical tubes, with the condensate in laminar flow can be expressed as :
hshell = hshellv = 1.47*[λ3*ρ2*g/μ2]1/3[(4*Gv) / μ]-1/3
Condenser Design Calculation Excel Spreadsheet
With
Air Cooled Condenser Design Calculation Excel
hshellv = heat exchange coefficient on the shell side for vertical tubes (W.m-2.K-1)
λ = thermal conductivity of the condensate fluid (W/(m.K)) (m⋅kg⋅s−3⋅K−1) - please refer to paragraph 2.6.1 for the calculation of Tfilm
ρ = density of the condensate fluid (kg/m3)
g = 9.81 m.s-2
μ = viscosity of the condensate (Pa.s) - please refer to paragraph 2.6.1 for the calculation of Tfilm
Gv = mass flowrate of condensate per unit of length of tube (kg/s/m) = mc / (π*do*Nt)
Horizontal tubes
hshell = hshellh = 1.51*[λ3*ρ2*g/μ2]1/3[(4*Gh) / μ]-1/3
With
Condenser Design Calculation Excel Example
hshellh = heat exchange coefficient on the shell side for horizontal tubes (W.m-2.K-1)
λ = thermal conductivity of the condensate fluid (W/(m.K)) (m⋅kg⋅s−3⋅K−1) - please refer to paragraph 2.6.1 for the calculation of Tfilm
ρ = density of the condensate fluid (kg/m3) - please refer to paragraph 2.6.1 for the calculation of Tfilm
g = 9.81 m.s-2
μ = viscosity of the condensate (Pa.s) - please refer to paragraph 2.6.1 for the calculation of Tfilm
Gh = mass flowrate of condensate per unit of length of tube (kg/s/m) = mc / (L*Nt)
2.5.3 Turbulent flow (Re < 10000)
Vertical tubes
hshell = hshellv = 0.0076*[λ3*ρ2*g/μ2]1/3[(4*Gv) / μ]0.4
With
hshellv = heat exchange coefficient on the shell side for vertical tubes (W.m-2.K-1)
λ = thermal conductivity of the condensate fluid (W/(m.K)) (m⋅kg⋅s−3⋅K−1) - please refer to paragraph 2.6.1 for the calculation of Tfilm
ρ = density of the condensate fluid (kg/m3) - please refer to paragraph 2.6.1 for the calculation of Tfilm
g = 9.81 m.s-2
μ = viscosity of the condensate (Pa.s) - please refer to paragraph 2.6.1 for the calculation of Tfilm
Gv = mass flowrate of condensate per unit of length of tube (kg/s/m) = mc / (π*do*Nt)
2.6 STEP 6 : calculation of the actual overall heat transfer coefficient Hcalculated
The heat transfer coefficient is the sum of the convection inside the tube, the conduction through the tubes, the convection outside the tube, also considering the fouling resistances on both sides of the tube. The actual overall heat transfer coefficient is thus :
Condenser Design Excel
+Support S.I Units/English (U.S) Units of measurement, Units converter containing 23 measurements and 200 units
+Import physical properties data to hot side and cold side from Microsoft Excel & from WeBBusterZ Physical properties database (included!)
+Save/Load results
+Export Results to Engineering Data sheet (excel, pdf formats supported)
+Export Results summary to Microsoft Word or Print Results summary.
Calculations
+Horizontal (shell side/tube side),Vertical (shell side/tube side) and Reflux condensers thermal design.
+Full/Partial condensation (Subject to condensation model selection please visit webbusterz for more).
+Sub cooling, super heated vapor, Zone analysis, Shear Controlled and Gravity Controlled condensation (Subject to condensation model).
+Basis and assumptions that the software makes during the calculations are stated on a visible panel.
+Support single phase vapor condensation on hot side and liquid coolant on cold side, bare tubes only
+TEMA designations.
+Calculate unknown Cold side temperature, Unknown Hot or cold side flow rate.
+Triangular and square pitch tube orientation
+Detailed results displays many calculated variables such as: Duty, Area, Number of tubes, Shell/Tube velocities, flooding velocity and operating velocity for reflux condenser, Reynolds numbers, Condensation heat transfer coefficient, flow regime, Number of Baffles and Baffle spacing, Scale resistance (dirt factor), Overall heat transfer coefficient for both Clean and Fouled conditions, Pressure drops...etc!
+Track calculation changes from trial to another
+Basic Physical Properties estimation database included as separate software (Contains 1450 components, free with full version)
+Add your own properties in the additional user databases
+Tube counts,standard tube sizes tables,Thermal conductivities..etc